How Testing of Plastics Enhances Safety and Environmental Impact
Plastics are ubiquitous in industries ranging from automotive and electronics to medical devices and packaging. While the versatility and cost-efficiency of plastics have revolutionized modern manufacturing, ensuring their safety and minimizing their environmental impact are paramount. This is where comprehensive testing of plastics plays a critical role. By conducting rigorous testing, manufacturers can ensure that plastic products meet stringent safety standards and contribute to a more sustainable future.
In this blog, we will explore how the testing of plastics enhances both safety and environmental sustainability, enabling manufacturers to produce high-quality, compliant, and eco-friendly products.
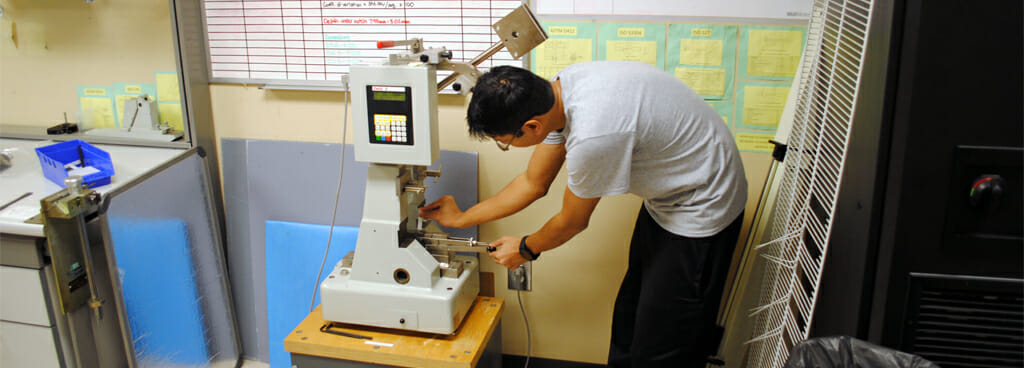
The Importance of Plastic Testing in Modern Manufacturing
Plastics offer manufacturers the ability to create products with exceptional durability, flexibility, and cost-effectiveness. However, the increasing complexity of plastic formulations and applications demands more thorough testing to meet both safety regulations and environmental standards. Comprehensive testing allows manufacturers to evaluate how plastics behave under various conditions and how they impact human health and the environment.
Balancing Performance with Safety and Sustainability
For many industries, the challenge lies in balancing the performance benefits of plastics with the need for safety and environmental responsibility. Advances in plastic testing methods have enabled manufacturers to meet this challenge head-on, ensuring that products are not only high-performing but also safe for consumers and sustainable for the environment.
Key Safety Aspects Addressed Through Plastic Testing
Ensuring the safety of plastic products is critical, particularly in industries like automotive, electronics, medical devices, and food packaging. Various plastic testing methods are employed to assess potential risks related to toxicity, flammability, and mechanical failure, among other factors.
1. Flammability Testing: Preventing Fire Hazards
Plastics are often used in applications where fire safety is paramount, such as in electronics, building materials, and automotive components. Flammability testing is essential to ensure that these plastics can withstand exposure to fire or heat without igniting or spreading flames.
Common Flammability Tests
- UL 94 Flammability Testing: This test classifies plastics based on their ability to resist ignition and control the spread of flames. It ensures that plastics meet regulatory fire safety standards, particularly in critical industries such as consumer electronics and building materials.
- Oxygen Index Test: This test measures the minimum concentration of oxygen required to sustain combustion in a plastic sample, providing insights into the material's fire resistance.
2. Toxicity Testing: Ensuring Consumer Safety
Certain plastic materials, especially when exposed to heat or chemicals, can release toxic substances that pose health risks to consumers. Toxicity testing is performed to assess whether a plastic product emits hazardous substances, such as volatile organic compounds (VOCs) or endocrine-disrupting chemicals, which may pose health risks.
Examples of Toxicity Testing
- Leaching Tests: These tests determine whether harmful chemicals, such as phthalates or BPA, leach out of plastics when in contact with food, water, or other substances.
- Outgassing Tests: These tests evaluate the emission of harmful gases or vapors from plastic products, particularly in confined environments such as cars or electronics.
3. Mechanical Testing: Preventing Failures and Injuries
Plastic products must be durable and strong enough to withstand mechanical stresses, especially in safety-critical applications such as automotive parts, construction materials, and protective gear. Mechanical testing methods help manufacturers evaluate the material’s strength, flexibility, and impact resistance to ensure that products do not fail during use, which could lead to injuries or accidents.
Key Mechanical Tests
- Tensile Strength Testing: This test measures the resistance of plastic materials to being pulled apart and provides insights into their strength and elasticity.
- Impact Resistance Testing: This test evaluates a plastic’s ability to absorb energy and resist breaking or cracking when subjected to sudden impacts, ensuring that products can handle unexpected forces without failure.
Addressing Environmental Impact Through Plastic Testing
In addition to safety, there is increasing pressure on manufacturers to reduce the environmental impact of plastics. From reducing plastic waste to minimizing toxic emissions, environmental testing is crucial for developing more sustainable plastic materials and processes.
1. Biodegradability Testing: Reducing Plastic Waste
One of the primary environmental concerns associated with plastics is their persistence in the environment. Biodegradability testing helps manufacturers determine how quickly plastic materials break down in natural environments, such as landfills, oceans, or composting facilities. This testing is essential for developing biodegradable plastics that can reduce the long-term accumulation of plastic waste.
Biodegradability Testing Methods
- ASTM D6400: This standard evaluates the biodegradability of plastics in composting environments, ensuring that materials can break down within a specific timeframe without leaving harmful residues.
- ISO 14855: This test measures the ultimate aerobic biodegradability of plastics under controlled composting conditions, providing insights into how quickly the material decomposes.
2. Recyclability Testing: Promoting Circular Economy
Recycling is a key component of the circular economy, where materials are reused and repurposed to minimize waste and resource depletion. Recyclability testing ensures that plastic materials can be effectively processed and recycled without degrading in quality. This helps manufacturers create products that are compatible with existing recycling systems and contributes to reducing the reliance on virgin plastic production.
Key Recyclability Tests
- Polymer Identification Testing: This method uses spectroscopic techniques to identify the polymer types in plastic products, ensuring that they can be properly sorted and processed for recycling.
- Material Degradation Testing: These tests assess how the material properties of plastics change after multiple recycling cycles, ensuring that the recycled material can still meet performance standards.
3. Microplastics Testing: Minimizing Environmental Contamination
Microplastics, small plastic particles that result from the breakdown of larger plastic items, are a growing environmental concern. They are found in oceans, freshwater systems, and even the air we breathe. Microplastics testing is crucial for understanding how plastics degrade and release micro-sized particles into the environment, enabling manufacturers to design materials that minimize this impact.
Microplastics Detection Methods
- Fourier Transform Infrared (FTIR) Spectroscopy: This method identifies and quantifies microplastic particles in environmental samples, such as water or soil.
- Microscopy and Image Analysis: These techniques allow researchers to visually identify and measure the size and distribution of microplastics in a sample, providing insights into how plastics degrade over time.
Regulatory Compliance: Ensuring Safety and Environmental Standards
Meeting regulatory requirements is essential for manufacturers that produce plastic products. Numerous industry standards govern the safety and environmental impact of plastics, and compliance testing ensures that products meet these strict regulations.
Key Regulatory Standards for Plastics
- REACH (Registration, Evaluation, Authorization, and Restriction of Chemicals): A European Union regulation that addresses the production and use of chemical substances in plastics to protect human health and the environment.
- RoHS (Restriction of Hazardous Substances Directive): A directive that restricts the use of certain hazardous substances, such as lead, mercury, and cadmium, in the manufacturing of electrical and electronic equipment.
- FDA Guidelines: For plastics used in food contact applications, compliance with the U.S. Food and Drug Administration (FDA) regulations ensures that materials do not pose risks to human health through contamination.
The Role of ISO and ASTM Standards in Plastic Testing
ISO (International Organization for Standardization) and ASTM (American Society for Testing and Materials) are leading organizations that set global standards for plastic testing. These standards ensure that testing procedures are consistent, reliable, and adhere to international best practices.
- ISO 527: Specifies the testing of the mechanical properties of plastics, such as tensile strength, ensuring material performance consistency.
- ASTM D256: Covers the testing of the impact resistance of plastics, crucial for evaluating how materials respond to sudden forces.
The Future of Plastic Testing: Moving Toward Safer and More Sustainable Materials
As industries continue to evolve, the future of plastic testing will focus on developing safer, more sustainable materials. Innovations such as AI-driven testing systems, real-time monitoring, and new biodegradable materials will play a key role in driving these advancements.
AI-Driven Testing for Enhanced Safety
Artificial intelligence (AI) and machine learning are beginning to play a role in plastic testing by analyzing large datasets to predict material behavior under various conditions. This will enable manufacturers to identify potential risks earlier in the development process, improving safety outcomes and reducing costs associated with recalls or failures.
Sustainable Plastics for a Greener Future
New materials, such as bioplastics and recycled polymers, are being developed to reduce the environmental footprint of plastics. These materials are designed to degrade more quickly or be recycled more efficiently, but thorough testing is needed to ensure they meet performance and safety standards while minimizing their impact on ecosystems.
Conclusion: The Critical Role of Plastic Testing in Ensuring Safety and Environmental Protection
Testing of plastics is not only crucial for ensuring product safety but also for reducing the environmental impact of plastic materials. By employing advanced testing methods, manufacturers can create plastics that are durable, compliant with safety regulations, and environmentally sustainable. As industries continue to innovate, plastic testing will remain a cornerstone of quality control, helping to enhance product performance while protecting consumers and the planet.